Fence Companies offer a one-stop solution for fencing projects. They build and install fences for homes, businesses, and commercial properties. They also sell various types of fencing materials.
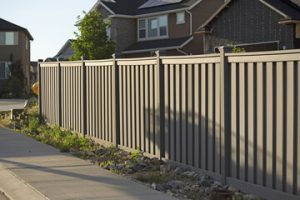
The best way to start a Fence Company is by choosing a limited liability corporation. This will provide protection in case of legal concerns.
One of the biggest factors influencing the cost of a fence is the type and amount of material used to construct it. The most common fencing materials are wood, vinyl, aluminum, and chain link, each with a different price point based on the cost of production and installation.
Wood fences are a popular choice for homeowners due to their natural aesthetic and versatility. However, they tend to be more expensive than other options. Additionally, wood fences must be regularly treated with pesticides and preservatives to prevent rot, mold, and insect infestations.
If you’re looking for a low-maintenance alternative, consider a vinyl fence. This durable material is available in a variety of colors and styles and is also resistant to rot and insects. It costs about $15 per linear foot to install a vinyl fence.
Another option is an aluminum fence, which offers a modern look similar to wrought iron and can be customized with various decorative elements. This type of fence is also more affordable than a traditional wrought iron fence.
The size and shape of your property will also influence the cost of a fence. A larger property will require a longer fence, which will increase the overall cost. Additionally, if your property is on a slope, it will need to be leveled before the fence can be built.
Other factors that can increase the cost of a fence include the complexity of the design and the availability of local labor. For example, a unique design can increase labor costs because it will require special tools or equipment. Also, a complex design can result in increased maintenance costs down the line. Additionally, if you live in an urban area, there may be additional costs associated with local regulations and permit fees.
Cost of Installation
The cost of a fence installation is influenced by a number of factors, including the type of fence, local labor rates, and location obstruction. If there are trees on the property, they may need to be removed and their roots cleared before a fence can be built, which is an additional cost. If the land is rocky, it can also be more expensive to dig fence-post holes. The fence installation company should be able to provide an estimate of the overall cost before work begins, but the final cost may vary depending on these and other factors.
A fence business can be a profitable venture if it is well run and if the right people are hired for the job. This is because they have the skills and equipment needed to complete the task efficiently. They also know what types of fencing materials are most popular in the area, so they can focus their efforts on supplying those materials. Moreover, they can offer the services of an accounting professional to manage the finances of the business.
Creating a successful fence company takes time, and it is important to develop a solid plan for the future of the business. Several companies offer franchise opportunities, which can help entrepreneurs who have no experience in this sector. This can be an effective way to minimize the risk and get started quickly.
Another strategy for starting a fence company is to join a trade organization, such as the American Fence Association, to receive discounts and educational opportunities. Many of these organizations also offer valuable networking opportunities. Some even award their members with the Blue Ribbon designation, which is a sign of excellence in the industry.
Cost of Insurance
The cost of insurance for a fence company depends on several factors, including the type of coverage purchased, the business’s location and size, and its industry risks. A fencing installation contractor should consider a comprehensive package that includes general liability insurance, workers’ compensation, commercial auto coverage for vehicles used in the business, tools and equipment insurance, and an umbrella policy. In addition, the business owner should consider the possibility of payment disputes with clients and whether or not to include professional liability coverage in the policy.
In most states, it is mandatory for fencing businesses to carry general liability insurance. This is designed to protect the fence company in the event of damage or injury caused by its employees, contractors, or products. This insurance will usually cover medical costs, repair or replacement expenses, and legal fees resulting from the incident. In addition, the insurance will typically cover any property damage to third parties or their possessions.
Another important aspect of fence business insurance is workers’ compensation, which covers the costs associated with injuries sustained by employees while on the job. It is also a good idea for fence companies to purchase excess liability insurance, which will provide additional protection in the event of a catastrophic loss.
Many companies choose to hire independent contractors rather than employ full-time employees. While this may be a more affordable option, it can lead to a number of problems. For example, independent contractors do not receive company benefits like health insurance or paid days off, and they may be less committed to the business. This can lead to poor workmanship, a lack of communication, and even theft.
In the case of a significant loss, it is essential to contact the insurance provider right away to initiate the claims process. The insurer will often send a claims adjuster to assess the damage or ask you to submit photos through their website or mobile app. Follow their instructions to ensure a smooth and hassle-free claim process.
Cost of Licenses and Permits
Fencing companies must obtain a variety of business and construction permits in order to operate. These may include zoning permits, building permits, and other government requirements. Additionally, fence installation businesses must obtain liability insurance, which protects against injuries and other damage to property during construction projects. Liability insurance is a necessity for any small business, and it can be purchased from numerous insurance companies. Before starting a fencing company, it is important to research the legal requirements in your state.
The cost of labor can be another significant expense for a fencing company. It is necessary to have extra hands on deck in order to complete projects quickly and efficiently. Fence companies can hire employees on a full-time basis or use temporary workers, depending on the needs of each job. It is also important to create a schedule for staff members so that they know when their paychecks will be issued.
In addition to purchasing materials and labor, a fence company must also pay for insurance and licenses. It is recommended to purchase general liability insurance, which covers damages that may occur to customers or to their property. In addition, it is also wise to buy worker’s compensation insurance, which covers medical expenses and lost wages in the event of an injury.
Another essential aspect of running a successful fence company is marketing. It is important to generate awareness of your services and make sure potential customers are aware of the various options available. This can be done through online advertising, print ads, or by putting up signage on local streets. In addition, a good marketing strategy should focus on targeting the demographics of your area. This will ensure that you get the most out of your advertising dollars.
Cost of Marketing
Fences are one of the largest items on the to-do list for most home owners. There is a huge market for new fences every year in modern American suburbia. This makes fencing a very profitable business model if you know how to position your company correctly in the local market and have a robust marketing plan.
Marketing costs include everything that you need to get customers to call you — like advertising, business cards, website, and phone numbers. It also includes any other ongoing expenses that you have to pay on a regular basis, such as vehicle costs, insurance, and employee wages.
A great way to reduce your marketing cost is to use software tools that help you save time and automate tasks. This can save you from expensive personnel costs and allows you to focus on attracting more clients.
Another way to cut your marketing costs is by using a lead generation company that can provide you with exclusive fence leads in your service area. These companies can help you reach more homeowners and sell your services quickly. However, you should always keep in mind that these leads may be more costly than direct sales from your website or referrals from existing clients.
When you talk to potential customers, emphasize the benefits of your services. Explain how your experience and skills will improve their yard’s curb appeal and security. Also, frame your pricing as an investment that will pay off in the long run. Finally, remember to ask previous clients for referrals, and reward them for their loyalty with a small service discount or gift card. Whatever marketing methods you choose, be sure to track their results over a 12-month period. This will allow you to see if they are working and make any necessary adjustments.