Plastics have revolutionized modern manufacturing and are used across a variety of industries. When searching for a plastic manufacturer, look for one that specializes in your industry and can offer dependable materials.
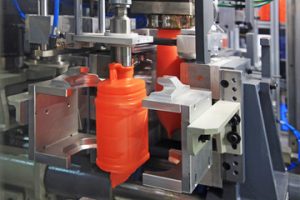
Plastic Manufacturers In Miami also work with industries such as defense and aerospace to produce specialized components and casings. For these types of projects, a manufacturer should have a deep understanding of regulations and quality standards.
Plastic manufacturing is a wide field with many different methods used for producing the final product. Some of the most popular techniques are injection molding, extrusion, blow molding, and rotational molding. Each process offers its own strengths and weaknesses, and it is important to find the right method for your product or project.
Injection molding is a commonly used technique that involves heating plastic granules to a molten state and then injecting them into a mold. Once the plastic is molded, it is allowed to cool and solidify before the mold is opened. This is a fast and cost-effective method for producing complex and high-precision plastic parts.
Another popular plastic fabrication method is extrusion, which produces long, continuous profiles such as pipes and hoses by forcing the molten liquid plastic through a die with a specific cross-section. This plastic production method is ideal for creating products with consistent dimensions, surface finish, and tolerances.
Blow molding is a similar plastic production method that uses air to expand and shape the melted plastic into a hollow form, such as a bottle or container. This plastic manufacturing process is fast and efficient for producing large, complex parts that require a hollow shape.
Rotational molding is a more complex plastic fabrication process that heats previously extruded plastic sheet to a pliable temperature before stretching it over a mould and trimming it to create the desired product. This method is used to produce products such as buckets, trays, and containers for the food and general retail industries.
As the concern over plastic pollution grows, sustainability will become an increasingly important issue in the industry. It is important to look for a plastic manufacturer that prioritizes waste reduction and utilizes recycled and biodegradable materials in its production processes. It is also important to ensure that all testing and quality control procedures are documented and accessible.
Raw Materials
The raw materials used in plastic manufacturing are sourced from various natural and organic sources like cellulose, coal, natural gas, salt, and, most commonly, crude oil. The extraction process is complicated, and the raw material needs to undergo a number of processes for further use in plastic production. The first step is to distill the crude oil in an oil refinery, which separates the heavier compounds from the lighter ones. This yields different petroleum products, including naphtha that is the raw material for plastic manufacturing.
The next step involves converting the petroleum compounds into monomers, which are the building blocks of plastics. There are many types of monomers, and each type has a specific set of characteristics and uses. Polyethylene is one of the most common monomers, which is used to produce a variety of plastics like bottles, bags, and food containers. Another popular monomer is polypropylene, which is used for pipes and other construction materials. Finally, polyvinyl chloride is another versatile plastic that is durable and offers a wide range of color options.
Plastic manufacturers need to carefully evaluate the source of their raw materials and consider the cost, quality, and availability. They should build strong relationships with suppliers and work closely with them to negotiate pricing and delivery terms. Additionally, they should optimize their production processes to reduce costs and minimize waste. Finally, they should monitor market trends and adopt sustainability initiatives to minimize their impact on the environment.
As the world becomes increasingly aware of the negative environmental impacts of plastics, governments and regulatory bodies may introduce new restrictions on plastic consumption and manufacturing. This could include limiting the use of certain types of plastics and encouraging recycling initiatives. Plastic manufacturers need to be prepared for these changes by developing closed-loop supply chains that minimize waste and reduce their dependence on raw materials.
Molding
The molding process involves a series of steps to transform raw materials into a finished product. It begins with the selection of a suitable material and then proceeds to the creation of a mold. The mould serves as the template for the product and is designed by an industrial designer or engineer. Once the mould is ready, it is used to form the final product using various forming methods.
Injection molding is a popular manufacturing method that uses thermoplastic or thermoset polymers. This process is especially suited to high-volume production of complex parts with tight tolerances and good material consistency. After the liquified plastic is injected into the mold, it is allowed to set and harden into the desired shape. The result is a high-quality, durable product.
This process is highly efficient, allowing manufacturers to produce parts with high accuracy and quality. It is also relatively inexpensive, requiring only an initial investment in the mold. It’s ideal for large-scale production and is commonly used in industries like food, automotive, and aerospace.
Blow Molding is another common manufacturing process that specializes in producing hollow plastic objects. It starts with a parison of plastic, which is then clamped into a mold. Air is then blown into the parison, inflating it to the mold’s shape. This produces a wide range of sizes and shapes, including double-walled constructions.
Rotational Molding, or rotomoulding, is a unique type of injection molding that focuses on creating large, hollow, one-piece parts. It begins with a parison of plastic, similar to blow molding. It then rotates on several axes, evenly distributing the liquid plastic. The results are stress-free, uniformly-shaped parts with very few seams.
Finishing
The final step in manufacturing is surface finishing. This is a crucial process that gives the product its appearance and enhances its durability. The surface of the product can be buffed, polished, coated, or etched to achieve specific textures and appearances. The type of finishing techniques that are used will depend on the product’s requirements, such as its ability to bond with other materials or to withstand a certain amount of wear and tear.
There are many ways to finish a plastic product, and it is important to choose the correct technique for each individual project. Some methods are time-consuming, while others can be completed instantaneously. These processes can have a significant impact on production schedules and supply chains. Choosing the correct finishing method will help to ensure that the finished product meets all required criteria, while also keeping costs low.
The plastics industry is a vital component of the global economy. Its innovative products and production techniques are constantly pushing the boundaries of what is possible, and its deep integration into global supply chains helps to drive economic growth and employment. This curated list of the top 10 plastic manufacturers highlights some of the most important players in this essential industry.
Quality Control
In the case of plastic manufacturing, quality control procedures are critical to ensuring that the final product meets or exceeds customer expectations and industry standards. These procedures can include inspections, testing, and documentation. These processes can help reduce product defects and ensure traceability of raw materials, which in turn helps manufacturers build customer trust and loyalty.
In addition to conducting regular quality control procedures, some plastic manufacturers use advanced technology to improve their quality assurance and control processes. For example, they may use non-destructive testing methods such as x-ray inspection or ultrasound to test products without damaging them. In addition, advanced sensors allow them to monitor and measure variables such as temperature and pressure in real time, enabling them to adjust production lines as needed. These technologies can also help them identify patterns and issues before they become larger problems, improving overall product quality.
One of the most important aspects of quality control in plastic manufacturing is raw material inspection. This involves evaluating and testing raw materials to ensure that they meet specific requirements before they can be used in the production process. This step can prevent costly mistakes by identifying and correcting any defects or flaws before the product is produced, saving both time and money.
Other quality control practices include using 3D printing to create prototypes of a product before starting full-scale production, and applying design for manufacturability (DFM) principles. This will help to make sure that the design is optimized for both production and long-term durability. In addition, many manufacturers use quality control software programs to track production metrics and provide data-driven insights into how to improve the quality of their products.