3D Printing uses computer-aided design to create three-dimensional objects through a layering process. This technique is often referred to as additive manufacturing.
The printing process involves melting, sintering, or solidifying the material in layers. Metals, thermoplastics, and even extracellular matrix materials can be printed. Contact 3D Printing Phoenix AZ now!
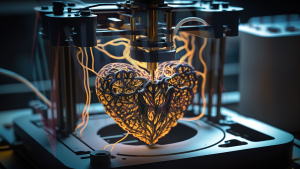
In addition, industrial 3D printing enables production to be localized on-demand, cutting logistics costs and reducing carbon emissions. It also allows for the production of spare parts directly where they are needed, reducing lead times.
Rapid Prototyping
The rapid prototyping process is an important step in designing and engineering new products. It allows designers to test a product’s functionality and design without risking a large investment in the creation of a mold. This process can also help to reduce production costs by minimizing the number of errors during the manufacturing stage. This is especially helpful for smaller businesses that cannot afford to spend a lot of money on creating a single prototype.
3D printing is an additive process that uses computer-aided design to create three-dimensional objects through a layering method. It can be used for a variety of projects, from simple prototypes to complex structures. The process can also be used for medical applications, such as making models of bones or joints. The resulting structures can be used to replace traditional surgical tools.
Prototypes can be created in a short period of time, and they are much cheaper than traditional forms of manufacturing. Injection molding, for example, can cost up to $800 per product. By contrast, a 3-D printer can produce a prototype for less than $15. It can even be used for functional testing, allowing engineers to make adjustments before the product is finalized.
The 3D printing process offers several benefits to businesses, including the ability to easily modify CAD files and reduce the amount of time needed for prototyping. It can also provide a quick way to get feedback from potential customers and investors. Moreover, it can increase productivity by reducing the need for costly molds.
Another advantage of 3D printing is the ability to use different materials for a single part. This can help to improve the strength of a part, and it can also reduce the weight of a finished product. This is especially useful for mechanical parts that need to withstand high stresses.
The printing process can also be used to create a range of textures and colors. This can give the finished product a more realistic feel and make it more appealing to consumers. In addition, it can allow designers to create geometries that would be difficult or impossible to create using traditional methods. This includes parts within parts and hollow areas in solid parts.
Cost-Effectiveness
3D Printing turns digital designs into real, touchable objects by stacking layers of materials. This cool technology is transforming manufacturing by making it cheaper and more efficient.
The cost of using this technique depends on the type of printer and the printing material used. The different types of 3D printers include Fused Deposition Modeling (FDM), Stereolithography (SLA) and Selective Laser Sintering (SLS). Each technology has its own set of raw materials, with some requiring other inputs like argon gas, isopropyl alcohol or mineral oil. Other factors that impact the cost of printing include design complexity, print volume and post-processing.
Another factor to consider is the energy required to operate the machine. The energy consumed is dependent on the size and complexity of the print, so choosing an energy-efficient printer can help to reduce costs. In terms of post-processing, the time and labor costs involved depend on the desired finish of the product. For example, sanding and painting are common post-processes, while polishing or assembly may require more specialised equipment.
Finally, jig and fixture costs can also be significantly reduced through part consolidation and the use of streamlined assemblies. This can lower production and maintenance costs, as well as reduce inventory and storage needs.
3D printing can be a great choice for low-volume production, particularly in the medical industry where it is being used to produce made-to-measure implants and devices. This technology is reducing the time it takes to get products to market, as well as cutting down on the costs of manual labour. It is even being used for the production of end-use parts in the rail industry, where bespoke components are being printed to repair worn parts. This is also a cost-effective alternative to traditional tooling and injection-molding, and can help to bring products to market faster. 3D printing is also opening up the possibility of mass customisation, allowing companies to create unique and tailored products that are right for their target markets. Ultimately, this can lead to more sales and profits. It can also improve customer satisfaction and boost brand image.
Customization
One of the biggest benefits of 3D printing is that it allows manufacturers to create customized products and parts. The technology is also highly flexible and can be used to produce a wide variety of different products without incurring the high cost and long lead times associated with traditional manufacturing techniques.
The ability to create unique product variations is especially beneficial for companies that offer products that require customization. For example, medical professionals can use 3D scanning and modeling to create custom prosthetics and orthotics for their patients. This personalization can help improve patient outcomes and increase customer loyalty.
Another benefit of mass customization is that it can help businesses to improve their supply chain and reduce inventory costs. Since 3D printing is a digital process, it can be easily scaled and used for small-batch production. It is also much faster than traditional manufacturing methods, making it a viable option for companies that need to deliver products to customers quickly.
In addition, 3D printing can help manufacturers to avoid unnecessary delays in production and shipping by reducing the need for tooling and assembly processes. This can cut down on production time and costs, resulting in higher productivity and lower overall manufacturing costs.
As the manufacturing industry evolves, more companies are embracing 3D printing to meet the needs of consumers. This is being driven by a number of factors, including the growing demand for personalized and tailored products. The technology is also becoming increasingly affordable, allowing companies to produce customized products more affordably.
Lastly, 3D printing can help to improve product performance and design by eliminating the need for molds and tooling. It can also be used to create complex geometries that may not be possible with traditional methods. This increased design freedom is helping to drive innovation and differentiation in the market.
Manufacturers are utilizing 3D printing to make a variety of different products and components, from automotive parts to medical devices. This new approach to manufacturing is changing the way that we think about production, enabling mass customization and revolutionizing how products are made. The possibilities are endless, and the future looks bright for manufacturers that embrace this new paradigm.
Reliability
The reliability of 3D printing has been a significant barrier to its widespread adoption. While the technology has improved, many manufacturers still have concerns about a lack of consistent quality and precision. This is especially important in highly regulated industries, such as aerospace. This is why companies are working on strategies to improve the reliability of additive manufacturing. These strategies include innovation, strategic collaborations, and efficient processes.
Despite the reliability challenges, 3D printing is already being used to solve real-world problems. For example, it is being used to create lighter and stronger components for automobiles, leading to increased fuel efficiency and improved performance. In addition, it is being used to print custom and specialized parts for older vehicles, allowing owners to maintain their cars with less effort. Furthermore, it is being embraced by the fashion industry to create unique and innovative clothing and accessories.
In medical applications, 3D printing is being used to produce patient-specific implants and surgical guides. This has the potential to improve patient outcomes and reduce the cost of healthcare. However, the accuracy of these devices depends on several factors, including the type of printer, materials, and the design of the part. The most common technique for printing medical models is stereolithography, followed by binder jet techniques, selective laser sintering (SLS), and fused filament fabrication (FFF).
The reliability of 3D printers also depends on the materials used. For instance, polycarbonate is a strong and resilient material that can withstand high temperatures and physical damage. Its reliability is influenced by the layer thickness and infill density, which determine the strength of the finished product. Higher layers and infill densities result in a stronger, heavier piece, but require more energy to process.
The accuracy of 3D printing is a concern for manufacturers, but it can be improved through the use of better quality printers and standardized materials. In addition, companies are implementing systems that enable them to qualify AM products more quickly and cost-effectively. This will help to address the barriers to adoption and make 3D printing more competitive in critical industries.